- Trendy
- Rozhovor
Konference Trends in Automotive Logistics 2024: V rychlém pruhu digitalizační dálnice
Digitální transformace je jako cesta, na kterou se musí podniky vydat, pokud se chtějí umět přizpůsobovat měnícím se podmínkám a získat konkurenční výhodu. Co vše potřebují „řidiči”, CEO, logistici a IT experti, k tomu, aby se…
Digitální transformace je jako cesta, na kterou se musí podniky vydat, pokud se chtějí umět…
Doporučené články
- Automatizace
- Článek
Potmě a efektivně: Dark warehouse jako budoucnost skladové logistiky
Skladová logistika je pro výrobní podniky vždycky výzvou. Pohyb velkého množství výrobků sice…
- SAP S/4HANA
- Článek
Téma podzimního setkání: Nejnovější trendy v systému SAP
Na konci minulého roku se v Plzni již tradičně sešli uživatelé jednoho z nejrozšířenějších ERP…
- Automotive
- Článek
Vyřešte B2G e‑Invoicing a získejte flexibilitu na mezinárodním poli
V dnešní digitalizované éře se podnikání neustále vyvíjí. Přechod na elektronické fakturování (e…
Automatizace
- Automatizace
- Článek
SCHERDEL – flexibilita jako klíčový cíl automatizace
In-house logistika je obtížnou věcí už u středně velkých společností. Jednou z nich je i firma…
- Automatizace
- Článek
Tlak trhu je tím největším katalyzátorem změn
Společnost Zebra Technologies, globální lídr a inovátor na poli automatické identifikace, provedla…
- Automatizace
- Rozhovor
S ředitelem logistiky společnosti LASSELSBERGER o úspěšném zavádění změn
Značka RAKO má na trhu tradici více než 140 let. Patří do skupiny Lasselsberger, která je jedním z…
Dostávejte souhrn novinek
ze světa logistiky, výroby a IT do mailu.
Přihlaste se k odběru Aimtec Insights
Přihlášením k odběru novinek souhlasím se zpracováním osobních údajů.
Digital Factory
- Digital Factory
- Článek
TAL 2023: Jak vypadá digitální transformace společnosti Safran
Smyslem každé změny v chodu firem by mělo být zlepšení, ať už z pohledu efektivity, nákladů či…
- Digital Factory
- Článek
Pět tipů pro úspěšnou digitalizaci plastikářské výroby
Plastikářská výroba je z pohledu digitalizace tak trošku oříšek, který je ale možné s úspěchem…
- Digital Factory
- Rozhovor
S automatizací se vytrácí flexibilita. Jak ji získat zpět, odpoví Rostislav Schwob z Aimtecu
Podle studie Trendy v české logistice 2022 plánuje automatizovat a pořizovat si stále…
Obsah ke stažení
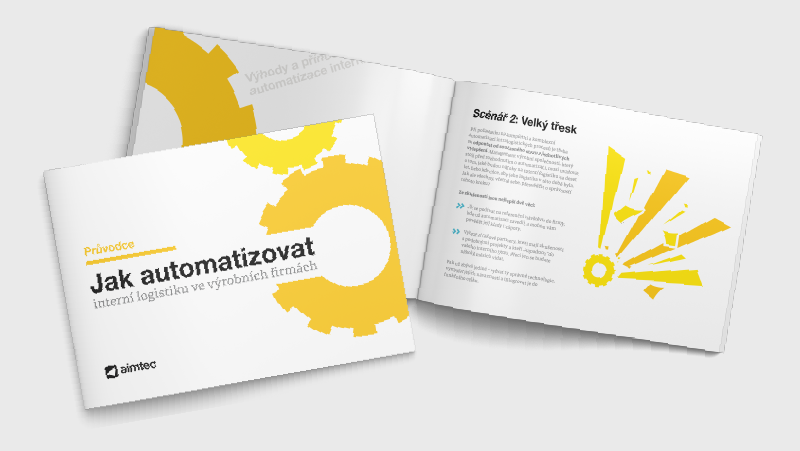
Jak automatizovat interní logistiku ve výrobních firmách
Efektivní využití lidské práce, úspora času, menší chybovost. To vše dokáže přinést automatizace interních logistických procesů výrobním firmám.
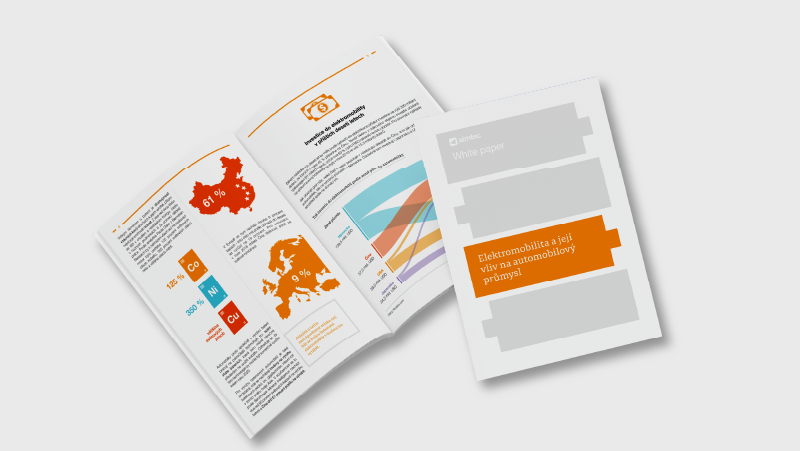
Elektromobilita a její vliv na automobilový průmysl
Stáhněte si tento white-paper, díky kterému pochopíte, co stojí za pravděpodobně největší změnou automobilového průmyslu od jeho vzniku.
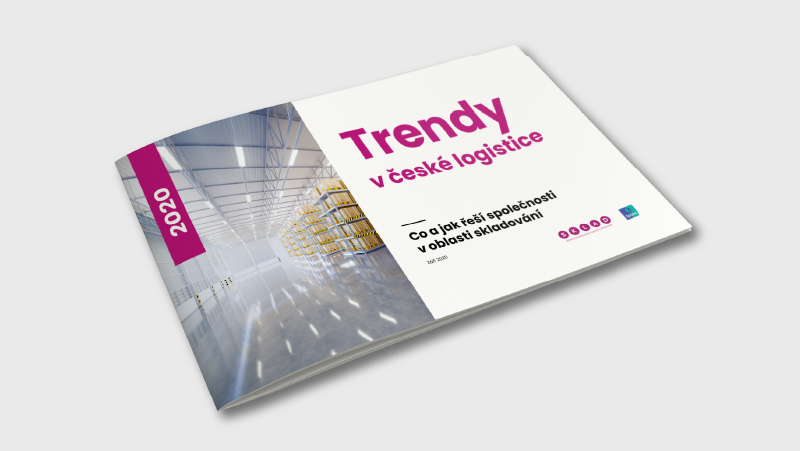
Trendy formující budoucnost logistiky
Stáhněte si zdarma jedinečnou studii, kde se dozvíte, jaké trendy budou podle českých logistiků formovat budoucnost oboru.
Čtěte také